Capping in a Clean Environment
The ST™ Cap Tightener
If you are capping in a clean environment you should consider our ST™ cap tightener. Constructed of 316 stainless steel, the ST™ cap tightener is ideal for use in laboratory, pharmaceutical, sanitary and and sterile packaging environments. 316 Stainless steel is the material of choice for these environments because it is easy to clean, resistant to corrosion, and is chemically resistant to the cleaning agents commonly used in these environments.
In addition to their 316 stainless steel construction, ST™ bottle cappers include other features that make them ideal for use in clean settings. The internal components of the ST™ capper are lubricated with NSF-H1 Food Grade Certified lubricants. The Kinex Exhaust Capture System™ is integrated into the design of every ST™ capping machine. As an option, the ST™ capping machine can be built with one of our oil free pneumatic motors. For more information on the ST™ cap tightener, please follow this link.
Oil Free Pneumatic Motors
Fit your PS™ Bottle Capper with an optional oil free pneumatic motor. Just as the name suggests, our oil free pneumatic motors do not require lubrication. An oil free pneumatic motor can be installed in an ST™ capping head and a standard SA™ capping head.
Standard pneumatic motors cannot be used in many clean environments because they expel a tiny amount of lubrication in their exhaust. Although the amount of oil they expel is so minimal that it is completely imperceptible, they still may not be suitable for some clean environments.
Our oil free motors require no lubrication, ensuring the exhaust air exiting the machine is as clean as the compressed air going in, while maintaining the same proven reliability and performance as our standard pneumatic motors.
Exhaust Capture System™
The Exhaust Capture System™ is an optional enclosure that captures the compressed air exhausted by the capping motor and channels it directly into an air hose. The exhaust air then travels through the air hose to where it can be expelled in a location that will not adversely affect the clean environment.
A PS™ Capping Machine with the Exhaust Capture System™ is shown to the right. There are two coil air hoses that enter the rear of the capping motor. The incoming compressed air travels through one of the coil air hoses while the exhaust air travels through the other. If you look at the column of the capping machine closely, you can see two air lines running parallel to the column. One is the air supply line while the other is the exhaust air line.
The Exhaust Capture System™ can be installed on both our standard and oil free pneumatic motors.
Machined Chucks
The urethane or white rubber chuck inserts within a standard chuck will wear slowly over time and can occasionally leave very small amounts of urethane or white rubber particles on the caps they tighten. These particles may not be allowed in certain clean, sterile or controlled environments.
Machined chucks are ideal for clean environments because they do not wear or generate particles. Machined chucks are custom made to fit the rib pattern of a specific cap, much like a socket fits a nut. They improve torque accuracy and never have to be replaced. Machined chucks are commonly fabricated from aluminum, various grades of stainless steel, or plastics, depending on which material best suits the production environment in which they will be used.
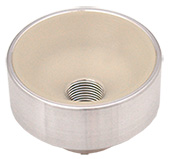
Standard Chuck
With Urethane Liner
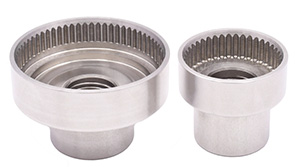
Machined Chucks
Cap Retaining Machined Chucks
A cap retaining chuck is a machined chuck that is designed with additional features that allow it to grasp and retain the cap it is designed to work with. Below are a couple of examples of applications in which they are useful.
- De-cap and Re-cap Operations
When decapping a container using a cap retaining chuck, the cap remains in the chuck after it has been removed from the container. This makes it ideal for use when you want to reapply the cap that has been removed. - Pick & Place Operations
Cap retaining chucks can be used to pick up a cap, hold it, and then tighten it onto a container. For this reason they are ideal for use with automated capping machines and automated robotic capping systems.
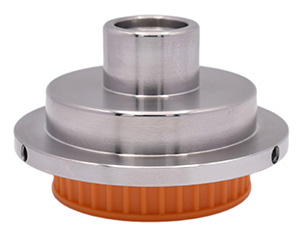
Cap Retaining Chuck